- Posted on: 2020-02-04
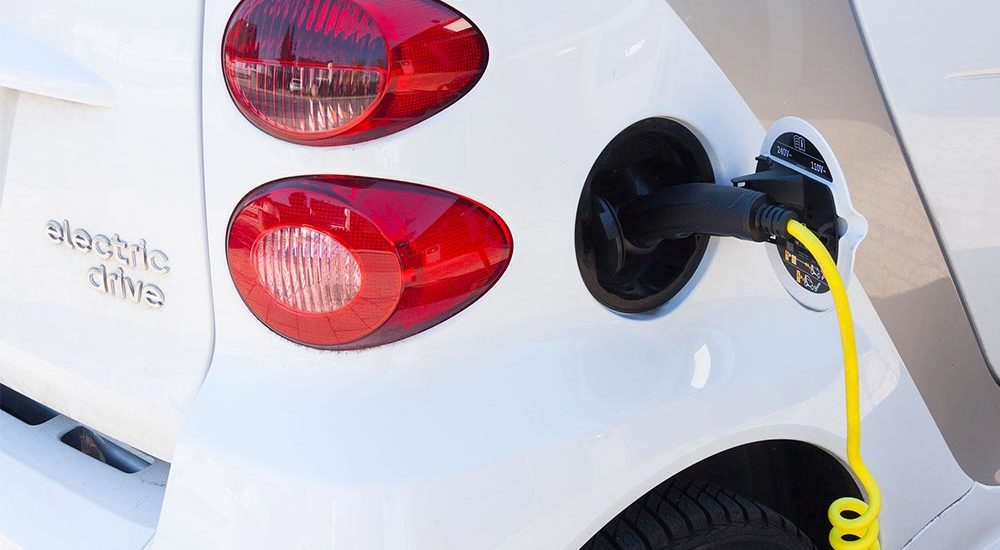
An embedded system is a controller with a dedicated function within a larger mechanical or electrical system, often with real-time computing constraints. It is embedded as part of a complete device often including hardware and mechanical parts. Embedded systems control many devices in common use today. Ref: Wikipedia
Problem: Test and validation of embedded systems is difficult and will become more so as product complexity increases, and development cycles shorten. To become more successful, electronic manufacturers need innovation in device function, and acceleration in research, development and production testing.
Solution: Achieving those depends on the skill of their designers and the effectiveness of their test systems. With optimal Automated Test Systems (ATS), engineers can focus on development rather than troubleshooting. In this post (and the linked whitepaper) we use a newly developed Battery Management System (BMS) as an example, to show how you can enhance National Instruments LabVIEW-based simulation and modeling to get testing answers and insights in less than 60 seconds, 24/7. In the whitepaper the use case is simplified to the 3 steps indicated in the figure below For test managers and teams technically interested in the full use case, this blog post shows how the proposed ATS investment can be leveraged in a full BMS development, including development of the Pack Controller and other components (not shown in image).
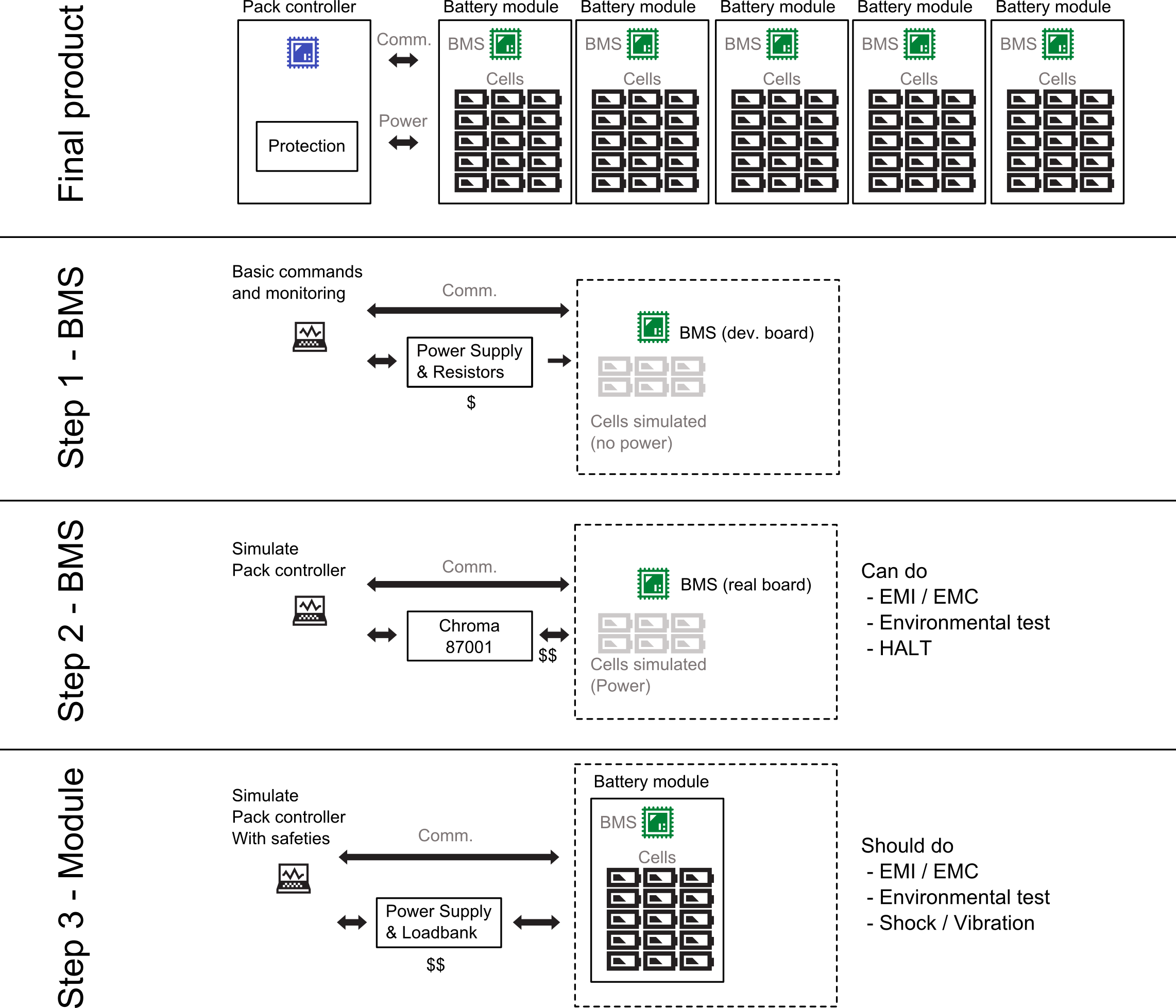
The Full BMS Use Case:
A client in the battery space told us that a test that would take them 2 hours to perform on a real cell now takes them only one minute with the cell simulator and Symplify™ script engine.
A cleantech manufacturer wants to bring new rechargeable lithium-ion batteries to the market. The engineering manager tasks experienced design engineers to design the BMS that will be responsible for:
- Monitoring the status and health of the cells
- Reporting cell voltages, temperature, state of charge (SoC), State of Health (SoH)
- Communicating with other embedded components via CAN network
- Protecting the battery
By relying on Automated Test Systems (ATS) earlier in the development of new products, our clients can reduce troubleshooting time by more than 75%, mostly from:
- Offering centralized and synchronized control and data from multiple instruments
- Getting repeatable test results
- Reducing test time by up to 90%
- Comparing quickly test results from different firmware versions
- Testing automatically all the safety features of their product multiple times a day
You should read our White Paper for the entire story on how you can accelerate BMS development which is also applicable to other types of embedded products. The explanations and trade offs will help guide you to select the right solution in your situation among:
- Continue to use your existing simple ATS (or manual testing)
- Extend your existing ATS system or personnel
- Move to a testing platform that extends, enhances and automates your existing ATS.